Last Updated APRIL 2025
Maximizing Operational Efficiency: The Critical Role of Hygiene in Industrial Facilities
Unlock the secret to operational efficiency by making hygiene a strategic priority. Learn how small changes in cleaning practices can drive productivity, reduce downtime and enhance safety — for a more streamlined and successful facility.
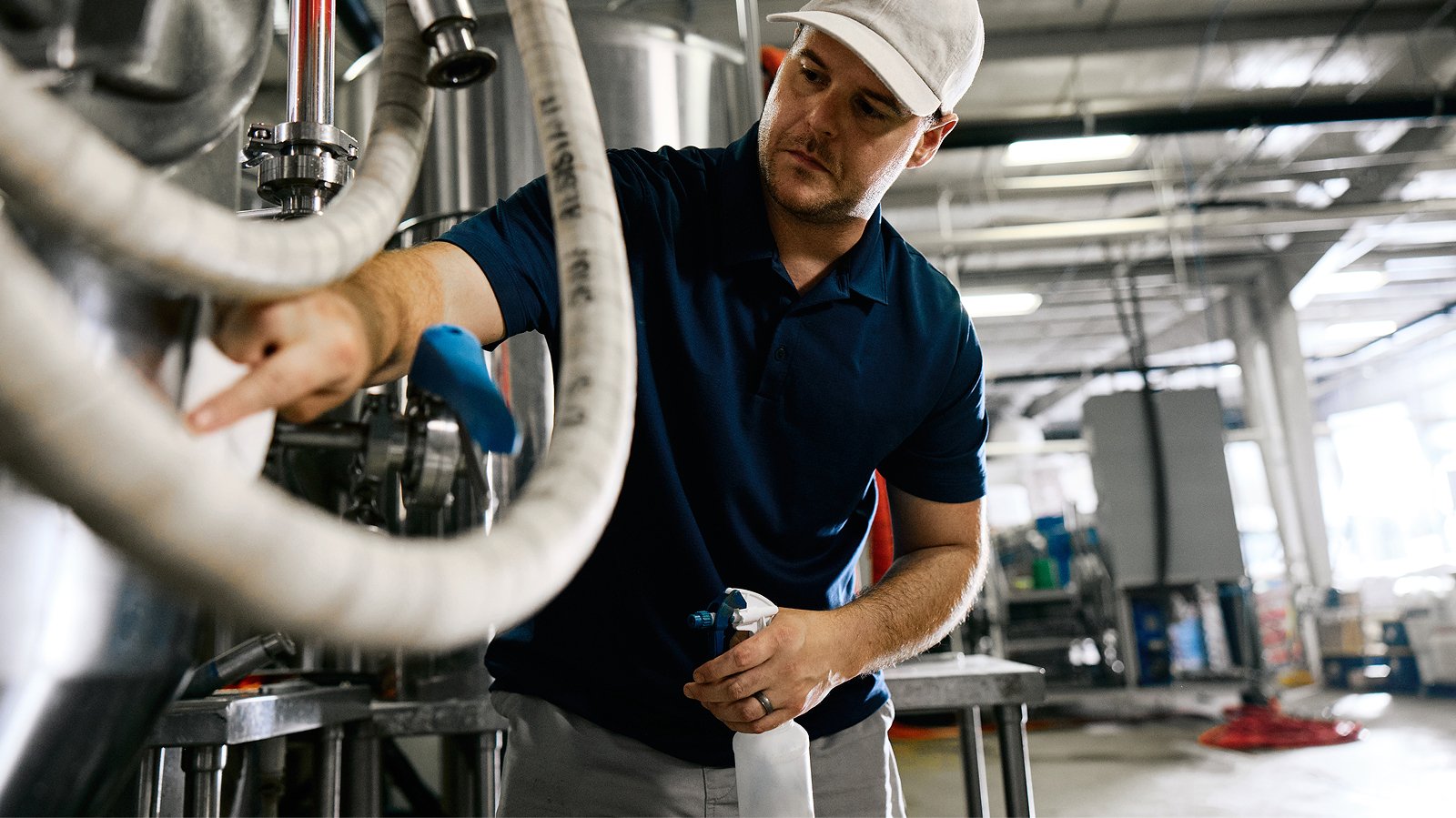
Operational efficiency extends beyond just processes and equipment; it’s about the people and practices that ensure everything runs smoothly. Hygiene plays a pivotal role in this equation, reducing downtime, enhancing productivity and maintaining safety and compliance. Workplaces with higher hygiene standards experience up to 80% fewer instances of productivity loss due to illness.1
Let’s explore how you can incorporate hygiene into your operational strategy to maximize efficiency across your facility.
6 Hygiene Tips to Drive Operational Efficiency
1. Recognizing Hazards and Safeguarding Operations
In industrial facilities, identifying and addressing potential hazards is critical for both safety and efficiency. While compliance is important, going beyond minimum requirements to proactively identify and mitigate risks can significantly reduce downtime and improve operational continuity.Poor maintenance practices, such as unaddressed buildup or contamination, not only create safety risks, but also lead to unnecessary operational disruptions. Unplanned downtime costs industrial facilities billions annually, with estimates ranging up to $50 billion across the manufacturing sector due to poor maintenance practices.2
Proactive hygiene practices, combined with regular risk assessments, can help mitigate these costs by reducing the likelihood of equipment failure.

2. Preventive Maintenance: A Proactive Approach to
Regular cleaning is a key part of any preventive maintenance strategy, helping to prevent buildup and wear that can lead to costly disruptions. By addressing contamination with effective cleaning solutions, facilities can maintain machinery reliability and extend equipment lifespan.While predictive maintenance tools help forecast failures, routine cleaning reduces the risk of issues before they arise. This proactive approach ensures equipment operates efficiently and minimizes the risk of downtime.
3. The 5S Framework: Organizing for Operational Success
The 5S principles — Sort, Set in Order, Shine, Standardize, Sustain — are essential components of the Lean manufacturing methodology, aimed at creating a clean and efficient workspace. By integrating hygiene into each principle, you streamline operations and promote a culture of continuous improvement.- Sort: Remove unnecessary items to reduce clutter and improve safety, ensuring only essential cleaning supplies are available.
- Set in Order: Organize tools, equipment and cleaning supplies for easy access, reducing downtime.
- Shine: Clean regularly to prevent contamination and ensure equipment runs smoothly, minimizing disruptions.
- Standardize: Establish consistent cleaning protocols and schedules to maintain cleanliness and reduce operational interruptions.
- Sustain: Foster a culture of cleanliness and organization through regular training and continuous improvement.
Effective maintenance is a natural outcome of applying the 5S principles. Studies show that poor maintenance can reduce capacity by 5% to 20% — a significant cost for any facility.3

4. Educating and Empowering Employees
Maintaining hygiene standards is essential for operational efficiency. When employees understand how hygiene directly impacts productivity and safety, they are more likely to take ownership of cleanliness.Providing tools such as touchless dispensers, strategically placed sanitation stations near key work zones and creating standardized cleaning protocols that are clearly communicated to employees ensures hygiene practices are consistently followed.
Empower your team with the right tools and training to help reduce contamination risks and minimize long-term costs associated with unplanned downtime.
5. Reducing Germ Spread: A Critical Element of Efficiency
Workplace illness can lead to absenteeism, disrupting operations and delaying production schedules. In restrooms, which are likely among the busiest, yet often most overlooked, spaces in the entire facility, preventing the spread of germs is critical to maintaining workforce health and operational efficiency.Research shows that unplanned downtime costs industrial manufacturers as much as $50 billion a year, with shutdowns consuming up to 1%–10% of available production time.4
To help reduce the spread of germs provide sanitization stations near key work zones, utilize touchless dispensers in restrooms and adopt needs-based cleaning schedules.
By maintaining a clean environment and promoting proper hygiene, you can reduce absenteeism and help keep your workforce healthy and productive.
6. Leveraging Smart Solutions for Efficiency
Utilizing smart restroom solutions like Onvation® puts data at your fingertips, allowing you to optimize cleaning schedules and improve resource allocation. These innovations are a game-changer for operational efficiency, offering insights that reduce waste, improve labor distribution and help maintain higher hygiene standards.By leveraging data-driven technologies, you can easily identify usage and cleaning patterns, cutting labor costs and minimizing product waste where it’s needed most.
The Bottom Line: Hygiene as a Key Driver of Operational Efficiency
Integrating hygiene into your operational strategy is more than a compliance measure — it’s an investment in efficiency and productivity. By adopting proactive hygiene practices and leveraging smart solutions, you can mitigate risks, reduce downtime and improve workforce health, all while keeping your facility operating at peak performance.
[Infographic] Maximize Operational Efficiency with Hygiene
Download the infographic to see how integrating hygiene practices into your operational strategy can reduce downtime, boost productivity and enhance safety. Share these actionable tips to help maintain a more efficient facility.
2 The Wall Street Journal. (n.d.). Unlocking Performance. Emerson. https://partners.wsj.com/emerson/unlocking-performance/how-manufacturers-can-achieve-top-quartile-performance/
3 Deloitte. (n.d.). Predictive maintenance and the smart factory. https://www2.deloitte.com/content/dam/Deloitte/us/Documents/process-and-operations/us-cons-predictive-maintenance.pdf
4 Ravande, S. (2022, February 23). Unplanned Downtime Costs More Than You Think. Forbes. https://www.forbes.com/councils/forbestechcouncil/2022/02/22/unplanned-downtime-costs-more-than-you-think