Última actualización ABRIL 2025
¿Conoces el verdadero costo del tiempo de inactividad de tus instalaciones?
Una de las principales tareas de la jornada laboral de un gerente de producción de la industria manufacturera es gestionar el tiempo de inactividad. Cuando se gestiona bien, el tiempo de inactividad puede ayudar a aumentar la eficiencia, la producción y la rentabilidad.
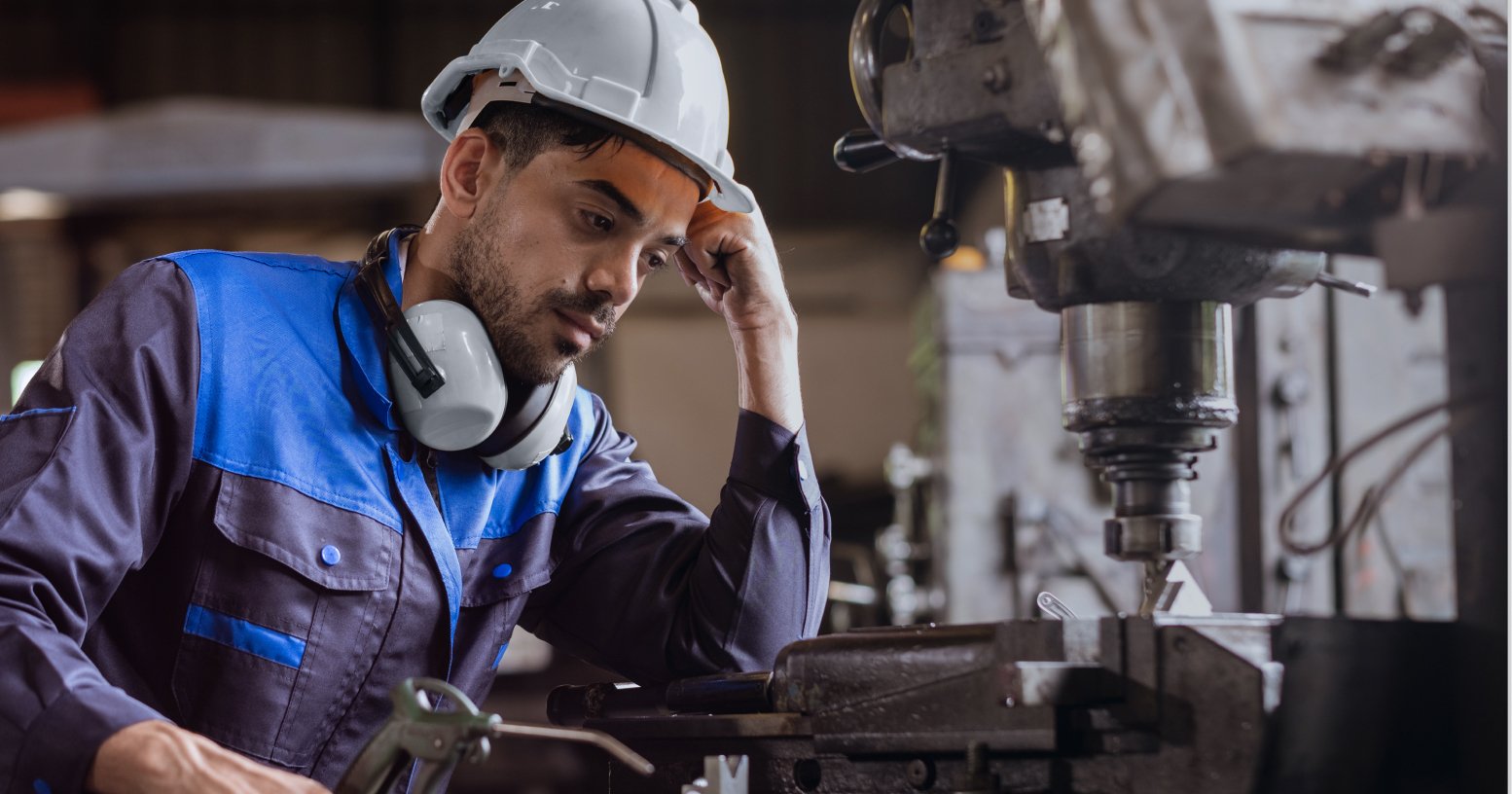
Sin embargo, cuando este se gestiona mal, puede afectar la producción y crear diversos problemas posteriores hasta que se encuentre una solución.
Dato conocido:
El tiempo de inactividad en manufactura es costoso.
Dato menos conocido:
Más del 80 % de las empresas no pueden calcular correctamente sus costes reales de tiempo de inactividad1.
El tiempo de inactividad es inevitable en la fabricación, pero no todos los tiempos de inactividad son iguales.
El tiempo de inactividad planificado permite a los fabricantes detener intencionalmente la producción para gestionar de manera eficiente responsabilidades críticas, como el mantenimiento de la máquina, la limpieza de las instalaciones y los cambios de equipos, para maximizar el tiempo de actividad de la producción y mitigar futuras interrupciones.
El tiempo de inactividad no planificado ocurre cuando fallas inesperadas, como el mal funcionamiento de los equipos, fallas en los procesos y errores humanos, detienen la producción y afectan negativamente el tiempo de actividad y los ingresos hasta que se identifica y corrige el problema
Nombres similares, pero circunstancias muy diferentes.
Descubriendo los costos
Cuando el tiempo de inactividad planificado brinda la oportunidad de pronosticar el costo de detener la producción, el tiempo de inactividad no planificado solo se puede analizar después de la interrupción y si se dispone de información precisa sobre el rendimiento.
Para calcular el tiempo de inactividad no planificado como porcentaje del tiempo, es necesario:2
- Determinar el tiempo de funcionamiento planificado, en horas, para un período de tiempo específico y medible, como una semana, un mes o un trimestre.
- Realizar un seguimiento del número de horas de inactividad no planificadas experimentadas durante el período de tiempo determinado.
Luego, utilizando la siguiente fórmula, podrás calcular qué porcentaje del tiempo de funcionamiento planificado, se ve afectado negativamente por un tiempo de inactividad no planificado.
Tiempo de inactividad no planificado
Tiempo de operación planificado
Comprender el costo del tiempo de inactividad no planificado en términos de dólares perdidos, requiere un conjunto más completo de datos, que incluyen:3
- Tiempo de funcionamiento planificado (horas)
- Tiempo de funcionamiento real (horas)
- Número total promedio de unidades producidas (durante el tiempo de operación real)
- Beneficio bruto por unidad
Desde aquí, puedes ingresar los datos en la fórmula de cuatro pasos que se muestra a continuación.
Después de calcular el porcentaje de tiempo y el total de dólares brutos perdidos debido al tiempo de inactividad no planificado, puedes comenzar a establecer los puntos de referencia de rendimiento críticos necesarios, para medir la productividad futura y eliminar a tu empresa del más del 80% de las empresas que no pueden calcular correctamente sus verdaderos costos de tiempo de inactividad.
Reducir el tiempo de inactividad no planificado
Cuantificar el impacto del tiempo de inactividad no planificado es importante, pero implementar medidas correctivas es la forma de aumentar el verdadero valor de la productividad. Aquí hay tres acciones a tomar de inmediato:
- Proporcionar una mejor formación: Independientemente de sus años de experiencia, todos los empleados pueden beneficiarse de una formación continua para garantizar una mayor seguridad y productividad. El error humano es uno de los principales contribuyentes al tiempo de inactividad no planificado, por lo que mantener a su equipo preparado puede ayudar a reducir la cantidad de errores que detiene la producción.
- Optimizar los procesos de producción: Siempre hay margen para mejorar la forma en la que se realiza el trabajo. Desde planificar grandes gastos de capital, como actualizar la tecnología empresarial, hasta realizar ajustes incrementales, como garantizar el suministro adecuado de toallitas industriales para productos de limpieza y acabado en la planta de producción. Cada mejora que realice ayuda a optimizar el éxito futuro.
- Implementar la estrategia de mantenimiento correcta: Las malas prácticas de mantenimiento casi siempre resultarán en tiempos de inactividad no planificados. Ya sea predictivo, preventivo o reactivo, identificar e implementar la estrategia de mantenimiento adecuada para cumplir correctamente con el propósito en sus instalaciones, coloca a los fabricantes en el camino hacia un mejor tiempo de actividad y productividad.
Conozca más sobre la importancia de elegir la estrategia de mantenimiento adecuada para sus instalaciones.
Descargue nuestro eBook, Mantenimiento predictivo, preventivo o reactivo: ¿Está su estrategia alineada con el propósito correcto? hoy mismo.
Descargar ahora
1 The actual cost of downtime in the manufacturing industry, https://iiot-world.com/predictive-analytics/predictive-maintenance/the-actual-cost-of-downtime-in-the-manufacturing-industry/
2 How to calculate machine downtime, https://www.resco.net/learning/machine-downtime/
3 The Cost of Downtime (And How To Calculate Your Own), https://theupapp.com/the-cost-of-downtime-and-how-to-calculate-your-own/