Last Updated AUGUST 2023
Do you know the true cost of your facility's downtime?
Most manufacturing production managers will likely agree that managing downtime is a top workday priority. When managed well, downtime can help boost efficiency, production and profitability. However, when mismanaged, downtime can strain production and create various downstream issues until a solution is found.
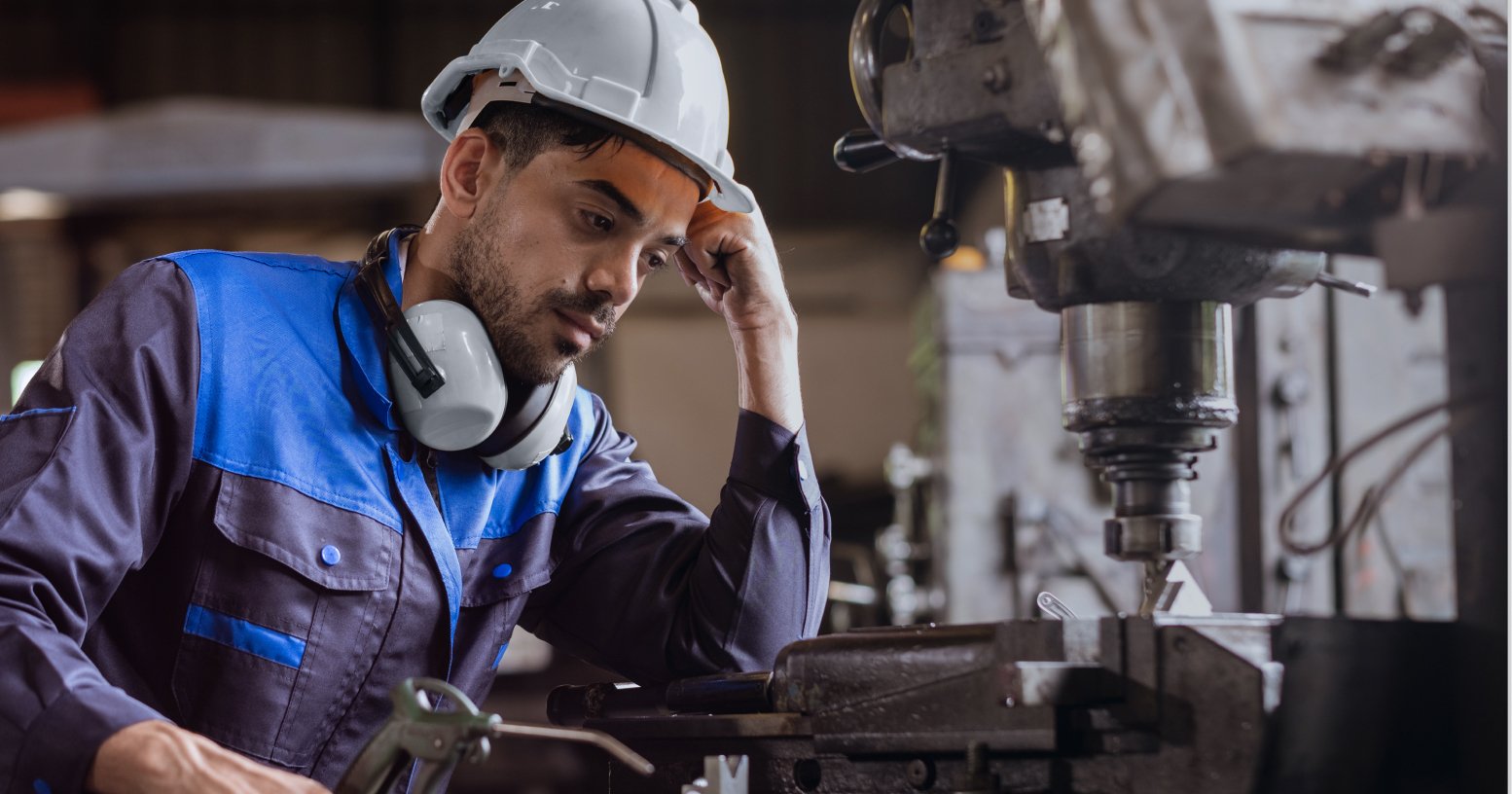
Known fact
Manufacturing downtime is costly.
Lesser-known fact
Over 80% of companies are unable to calculate their true downtime costs correctly.1
Downtime is inevitable in manufacturing, but all downtime is not the same.
Planned downtime allows manufacturers to intentionally stop production to efficiently manage critical responsibilities, like machine maintenance, facility cleaning and equipment changeovers, to maximize production uptime and mitigate future disruptions.
Unplanned downtime occurs when unexpected failure, such as equipment malfunction, process breakdowns and human error, halts production and negatively affects uptime and revenue until the issue is identified and corrected.
Similar names, but very different circumstances.
Uncovering the costs
Where planned downtime provides an opportunity to forecast the cost of stopping production, unplanned downtime can only be analyzed post-disruption and if accurate performance information is available.
To calculate your unplanned downtime as a percentage of time, you must:2
- Determine the planned operating time, in hours, for a specific and measurable timeframe, such as one week, one month or one quarter.
- Track the number of unplanned downtime hours experienced during the determined timeframe.
Then, using the formula below, you can calculate what percentage of your planned operating time is adversely affected by unplanned downtime.
Unplanned Downtime
Planned operating time
Understanding the cost of your unplanned downtime in terms of lost dollars requires a more comprehensive set of data points, including:3
- Planned operating time (hours)
- Actual operating time (hours)
- Average total number of units produced (during actual operating time)
- Gross profit per unit
From here, you can input your data points into the four-step formula shown below.
After calculating the percentage of time and total gross dollars lost to unplanned downtime, you can begin to establish the critical performance benchmarks needed to measure future productivity and remove your business from the over 80% of companies that are unable to calculate their true downtime costs correctly.
Reducing unplanned downtime
Quantifying the impact of unplanned downtime is important, but implementing corrective measures is how true productivity value is increased. Here are three actions to take immediately:
- Provide better training: No matter their years of experience, all employees can benefit from continuous training to ensure better safety and productivity. Human error is a major contributor to unplanned downtime, so keeping your team prepared can help reduce the number of production-halting mistakes.
- Optimize production processes: There is always room to improve the way the job gets done. From planning large capital expenditures, like upgrading enterprise technology, to making incremental adjustments, such as ensuring you have the right supply of industrial wipes for cleaning and finishing products on the production floor. Every improvement you make helps to optimize for future success.
- Implement the right maintenance strategy: Poor maintenance practices will almost always result in unplanned downtime. Whether it’s Predictive, Preventive or Reactive, identifying and implementing the right maintenance strategy to fulfill the right purpose in your facility puts manufacturers on the path to improved uptime and productivity.
Learn more about the importance of choosing the right maintenance strategy for your facility.
Download our eBook, Predictive, Preventive or Reactive Maintenance: Is your strategy aligned with the right purpose?, today.
Download Now
1 The actual cost of downtime in the manufacturing industry, https://iiot-world.com/predictive-analytics/predictive-maintenance/the-actual-cost-of-downtime-in-the-manufacturing-industry/
2 How to calculate machine downtime, https://www.resco.net/learning/machine-downtime/
3 The Cost Of Downtime (And How To Calculate Your Own), https://theupapp.com/the-cost-of-downtime-and-how-to-calculate-your-own/