Last Updated JULY 2023
Putting Safety First Increases Productivity and Efficiency
Safety at work is important when it comes to improving productivity and efficiency. Keeping your employees engaged gives them ownership and makes them more accountable when it comes to being safe in the workplace.
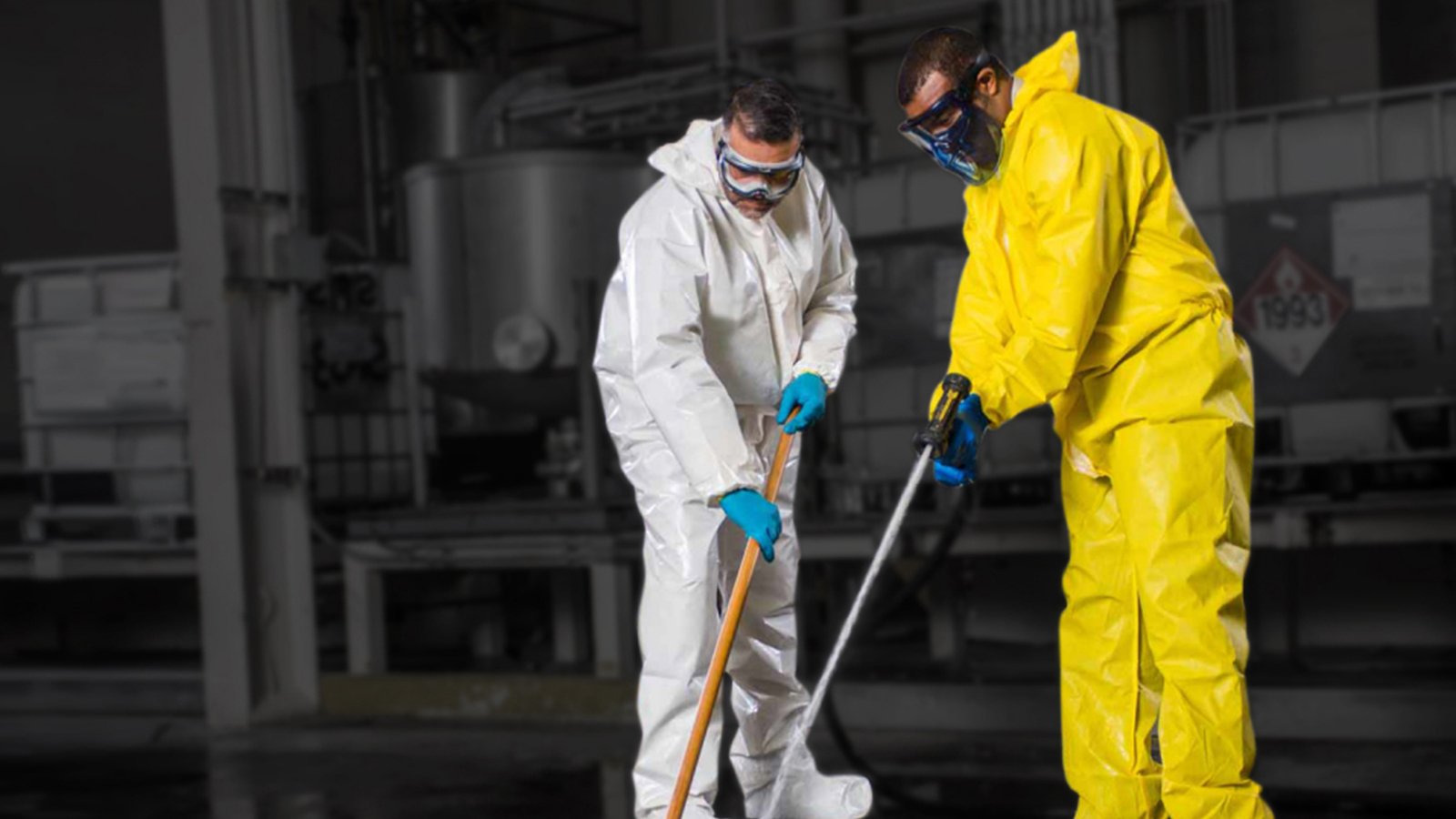
“There are attitudinal barriers around building a culture of safety-based behavior,” says Lena Heidel, global industrial business manager for Kimberly-Clark Professional. “Companies fear that it will harm operational results, not improve them.” For example, a production manager may overlook safety measures fearing that they might disrupt productivity or increase costs.
“We continue to see a need to change safety-based behaviors in the manufacturing environment,” says Mazen Kachlan, Global KleenGuard Brand Leader for Kimberly-Clark Professional. “There is a belief that employee safety and operational results are mutually exclusive and therefore a production manager may prioritize operational results over safety. We find that the contrary is true, instilling a strong safety culture leads to greater efficiency and better business results."
"If anything, emphasizing safety and optimizing performance leads to greater efficiency in the workplace", Heidel says.
For years, the Kimberly-Clark facility in Corinth, Mississippi, maintained a strong safety record. Then suddenly the facility started reporting notable incidents, like minor injuries and an increase in property damage. For Shannon Ross, a plant manager in the Kimberly-Clark Consumer Division, he knew that for the Corinth plant to be world-class in safety, it had to create a new safety culture.
“To accomplish this, we pulled together a cross-functional team to complete a four-step problem-solving session to analyze safety incidents that occurred during this time frame and get to the root cause,” Ross says.
During the session, Ross and his team discovered that employees didn’t feel engaged or accountable and didn’t have a sense of ownership in the workplace.
As a solution, Ross says "plant management encouraged every team member to commit to Kimberly-Clark’s Three Safety Obligations:
- I care about my safety.
- I care about the safety of others.
- I care about improving safety.
Everyone holds each other and themselves accountable for their safety.” This includes holding leadership accountable.
To foster behavior, change, the plant instituted five initiatives:
- Job Hazard Assessment Process
Team members were asked to stop and think before starting a work task and recognize factors, like fatigue, or pace changes that could compromise performance. - Safety Committee
The plant established a committee to collectively identify and assess specific hazards to determine the best ways to mitigate risk. - Leader Safety Visits
Leaders regularly conducted safety visits with teams to provide opportunities for real-time problem-solving. - Personalization of Safety
The management team shared personal and professional stories about workplace injuries to reinforce how vigilance benefits workers and their families. - Safe Behavior Scorecards
Team members were asked to complete scorecards tallying leading indicators and proactive measures (like safety visits), as well as lagging indicators and reactive measures (like writeups).
“Our team members were empowered and more invested in making sure that they and their co-workers were able to return home safely to their families each day,” Ross says.
The result: The Corinth plant emerged safer than before and even received Kimberly-Clark’s inaugural Corinthian Award for going 365 days without any major or minor injuries. The plant also significantly improved its efficiency. It realized year-over-year productivity gains of 9.5 percent and 7.9 percent in its folded and rolled wiper production lines, respectively.
In the end, the Corinth facility learned that by enacting incremental changes, encouraging open dialogue and taking a holistic approach to reinvigorate workplace culture, it could improve productivity and efficiency without sacrificing safety.