Last Updated MAY 2024
Streamlining Manufacturing Cleanliness
Streamlining Manufacturing Cleanliness: Best Practices for Optimal Operations
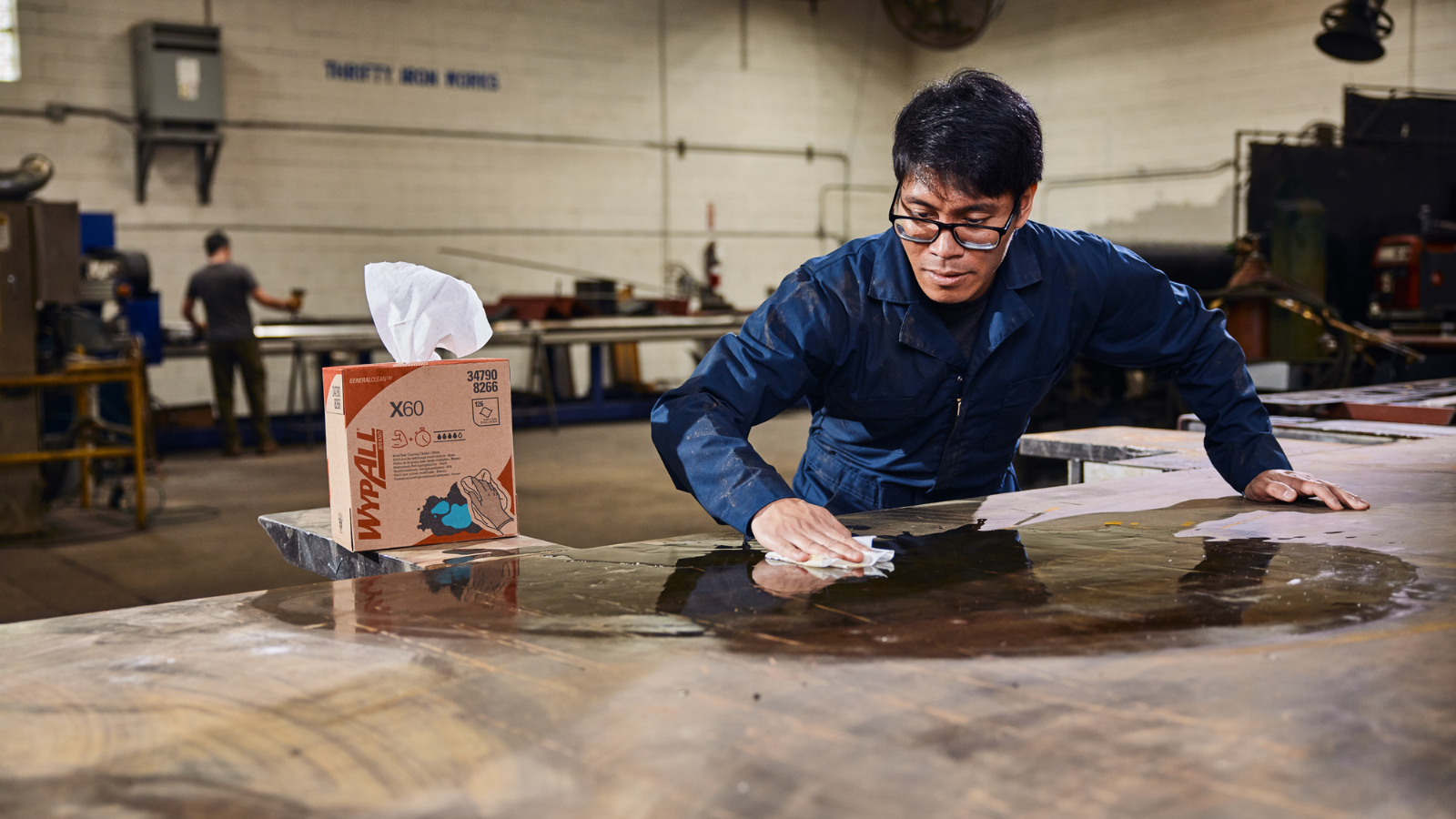
According to a 2021 survey, 89.9% respondents agreed that surface cleaning protocols are important in a workplace.2
Cleaning services have a major impact on product quality in manufacturing industries that require measures against cross contamination, stubborn grime, oil and grease. It is essential to avoid damage to a system’s function, or the functionality of a component 1. Implementing best practices in manufacturing cleanliness isn't just about sterilised surfaces; it's a comprehensive approach that harmonises processes with optimum use of correct industrial cleaning products and adhering to industrial cleaning protocols.
How do you ensure that you’re adhering to the best practices in industrial cleaning?
Here are some essential strategies to help you or guide you for an impeccable cleanliness standards at the workplace:
Structured Cleaning Protocols:
Establish a robust warehouse cleaning regimen tailored to different areas within the manufacturing site.
Employee Training and Engagement:
Empower your workforce with comprehensive training on cleanliness protocols and handling commercial cleaning equipment, emphasising on the importance of their role in maintaining a hygienic environment.
Strategic Product Selection:
Invest in fit for purpose industrial cleaning products and tools suited for diverse surface cleaning needs and equipment or machinery cleaning requirements. Ensure the compatibility of these products with equipment and materials used in the facility to reduce the risk of damage or contamination by consulting an expert, who can walk you through key improvement areas in your workspace3.
Routine Equipment Maintenance:
Regularly inspect and maintain industrial cleaning machinery and tools to prevent debris accumulation or wear and tear of equipment. Research suggests that over 80% of companies were unable to calculate their true downtime costs correctly.4
Adherence to Regulatory Standards:
Align your practices with industry-specific industrial cleaning regulations and standards.
According to the Cleaning Industry Management Standard Guidebook5,
it is recommended to have a Quality Plan – a written process to determine whether cleaning service requirements are met and to identify improvement opportunities.
Continuous Improvement and Assessment:
Implement a system for periodic audits and assessments to evaluate the efficacy of surface cleaning practices.
You can also book a consultation with our experts for a guided walkthrough of your workplace and receive valuable, personalised cleaning insights. Acquire a fresh perspective with Kimberly Clark Professional today!
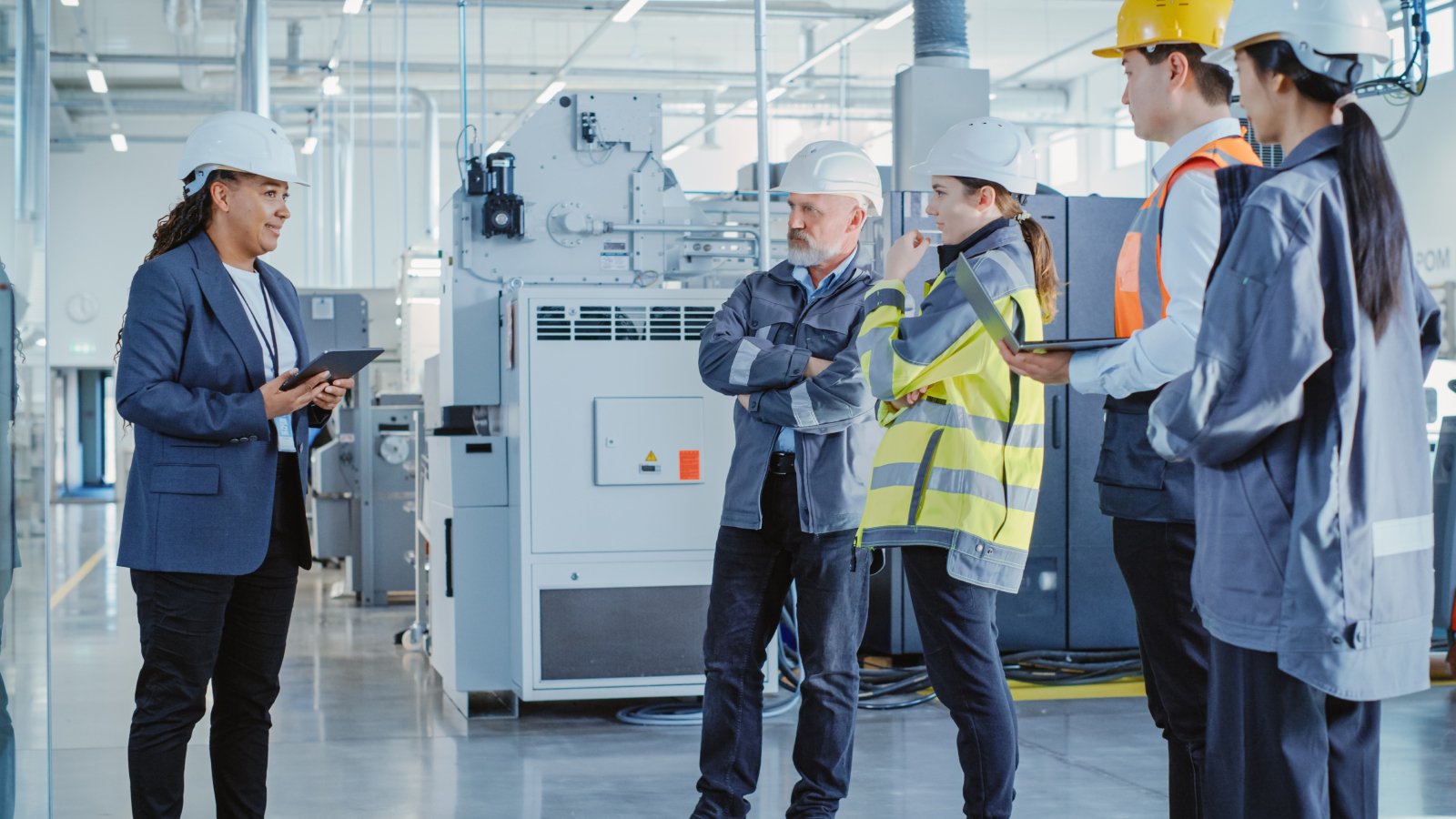
Want to know more about elevating the cleanliness of your workplace with specialised wiping solutions?
1 https://www.researchgate.net/publication/318112405_Research_on_importance_of_cleanliness_in_manufacturing_reliable_products_for_automotive
2 https://www.cleanlink.com/news/article/Study-Reveals-Link-Between-Clean-Workplaces-and-Employee-Satisfaction---30200
3 https://home.kcprofessional.com/uk/manufacturinghygiene
4 https://www.kcprofessional.com/en-us/workplace-insights/wypall/do-you-know-the-true-cost-of-your-facilitys-downtime
5 CIMS 3000: 2018, Effective March 2018 - https://www.aics.com/wp-content/uploads/CIMS-and-CIMS-GB-Combined-Guidebook-2018_03_18.pdf