Last Updated APRIL 2025
What are the best waste management options for industrial manufacturers?
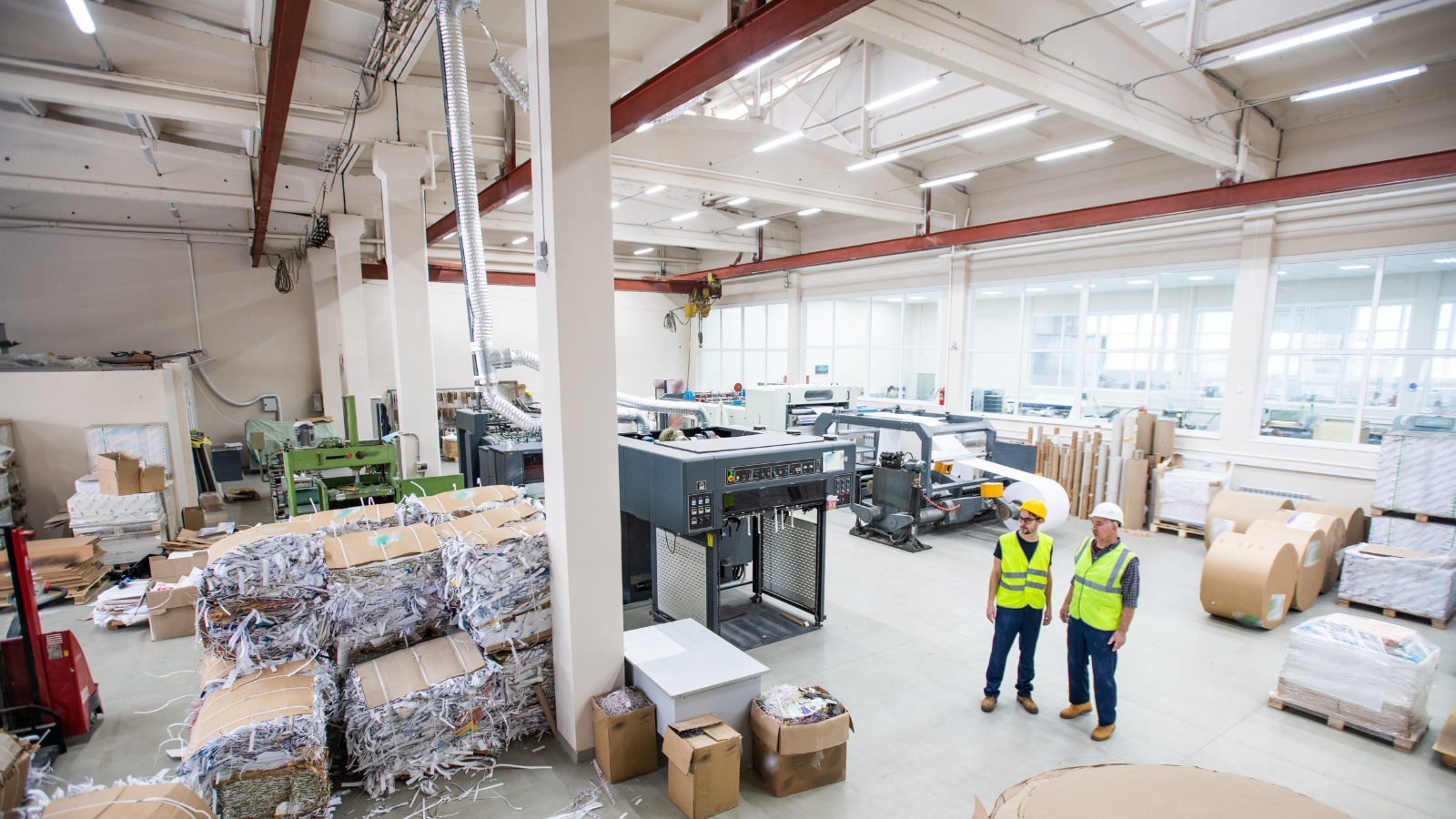
Industrial manufacturing creates a large amount of waste, from kiln ash and concrete to scrap metal, chemicals and solvents. Waste in this sector is usually a by-product of an industrial process. Thankfully, more and more industrial waste is recycled, with plenty of options available to reduce the environmental burden of commercial rubbish ending up in landfill or heading for incineration.
Addressing the recycling of plastics, metals, and paper, manufacturers have a myriad of options to integrate sustainable practices into their operations. Through mechanical recycling, partners can collect, sort and process plastic waste into reusable raw materials. Plastics can be cleaned, melted, and remoulded into new products, helping companies to conserve resources and reduce landfill waste.
More and more chemical recycling is also happening, with advanced technologies being used to breakdown plastic polymers into their molecular components which can then be used to produce new plastics or other chemicals, offering a closed-loop recycling solution.
Metals like steel, aluminium and copper are highly recyclable, with many manufacturers able to collect and process scrap metal, melt it down and reshape it into new products, reducing the need for virgin metals and lowering energy consumption. And given the ubiquity of electronics in industrial settings, recycling electronic waste – or e-waste – is crucial. Recovering valuable metals and components from discarded electronics mitigates environmental impacts and promotes resource conservation.
Kimberly-Clark Professional’s RightCycle™ Programme can help manufacturers reduce their overall waste footprint. Instead of old cleaning-wipe or hand-towel dispensers going into landfill, the previously hard-to-recycle items are collected at manufacturing sites and sent to a recycling partner which shreds the plastic units into pellets, reuses or melts down the metal screws, and ensures that all other parts are turned back into raw materials with nothing going to landfill or incineration. The RightCycle™ Programme also provides a closed loop recycling service for hand towels so that each used towel is turned back into new Kimberly-Clark Professional™ paper products, helping customers reduce their waste by up to 25% and increase their recycling rate by up to 5%.
Product take-back programmes are becoming more popular among manufacturers keen to support more environmentally conscious customers. By accepting old products to be returned companies are finding innovative ways to recycle, reuse or repurpose them.
Given the significant costs associated with energy, more and more manufacturers are exploring energy recovery systems as a way of using waste materials to power their facilities.
Not all waste is created equal, however. While industrial manufacturing has been a cornerstone of economic development, it has brought significant challenges, not least in the form of hazardous waste. The production processes inherent in many industries often generate waste which hazardous to human health. It must be dealt with through a combination of stringent regulations, specialised handling and responsible disposal practices.
As industrial manufacturing continues to play a pivotal role in driving economies all over the world, the management of waste is a critical consideration for both environmental sustainability and regulatory compliance. The increasing adoption of recycling initiatives, such as The RightCycle™ Programme, points to a progressive shift towards more responsible and efficient waste management practices within the industry.